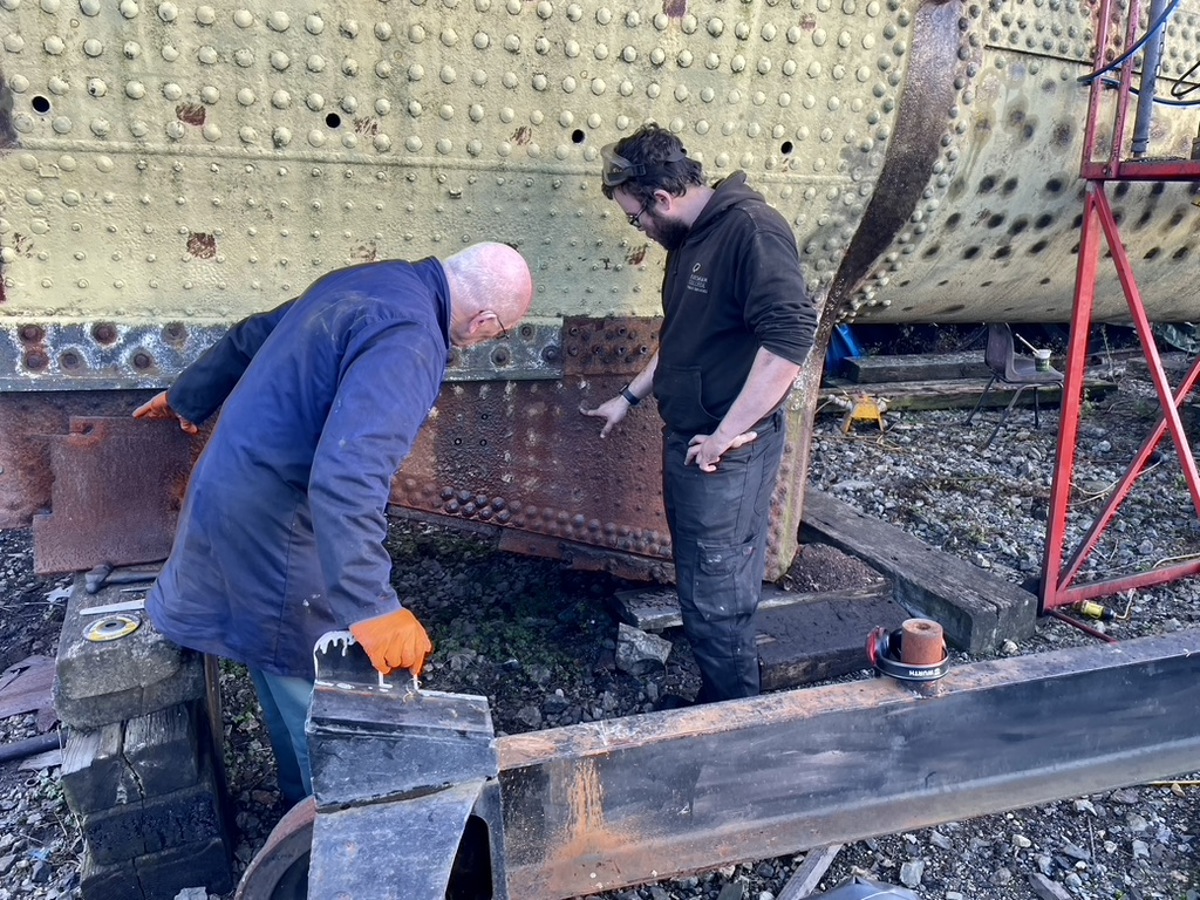
2024
For much of this year our volunteers (shared with other organisations based on the Gloucestershire Warwickshire Steam Railway) were heavily engaged in completing the overhaul of ex Great Western Heavy Freight 3850 and our project took something of a back seat. However, as our loco is an earlier version of 3850 we picked up a great deal of very useful information that we will use within our own restoration.
That said, we made some steady progress on a number of fronts:
The rear buffer beam assembly is now almost complete with the steps attached - a start has been made on the cab floor.
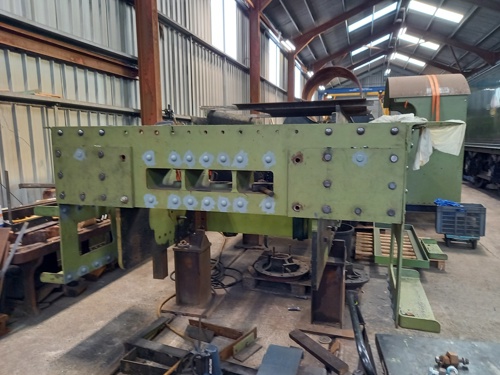
The eccentrics have been fitted to the driving axle and the sheaves have been machined to perfectly match these - next step is to mount the sheaves to the eccentrics.
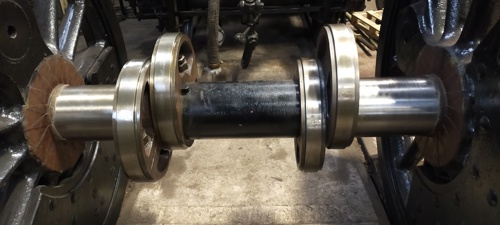
The machine shop has been busy working on both the new safety valve and completing the rocker arm housing assemblies

We were delighted to announce our award from the National Lottery Heritage Fund to train and develop volunteers in heritage engineering skills - with the focus of the project being those skills needed for boiler overhauls and repair.
We have a series of sub-projects concentrating on specific areas and have appointed two experienced contractors to supervise and train our volunteers in this complex area - and we have engaged British Engineering Services to provide the independent oversight that will lead ultimately to the required pressure vessel certificate allowing us to operate the locomotive.
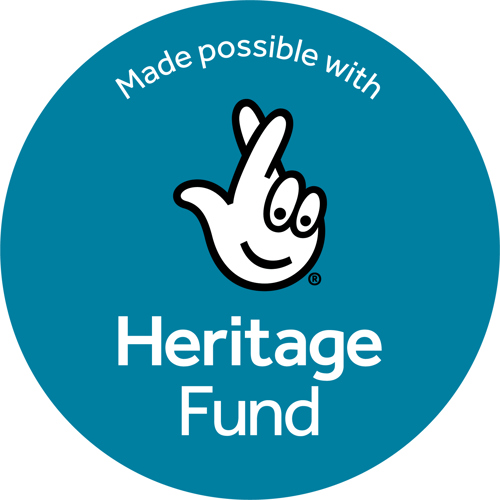
Tube Plate
An early task has been to remove the remains of the front tube plate - without damaging the boiler barrel which we anticipate being able to reuse. This involved the careful removal of the numerous rivets that hold it in place - and the weld that was added in British Railways days.
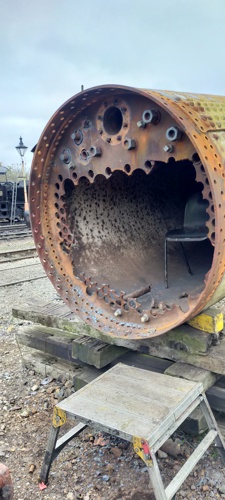
The image above shows the work in progress with most of the rivets removed and, forward of the tube plate remains, can be seen the holes where the smokebox spacer ring has come from - we will be able to reuse that ring - pictured below
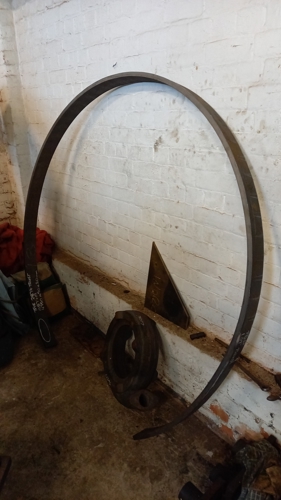
While all this was going on, the design and construction of the new tube plate was underway. The steel plate was water-jet cut, the flange bent to shape and both parts prepared for welding. The welding itself was carried out by Materials Engineering (UK) Ltd from Derby - an excellent job confirmed by extensive Non-destructive testing of the welds.
Tube Plate - ready for welding
The early work has been undertaken with the boiler on the ground - but we want to be able to move it around and we do need it turned over to complete the work on the lower part of the firebox. We engaged a specialist company who are familiar with this type of operation and proceeded to lift and turn the heavy structure. At the same time we mounted the boiler onto our (modified) accommodation bogies - we can now move the whole thing around the site - and even indoors when needed.
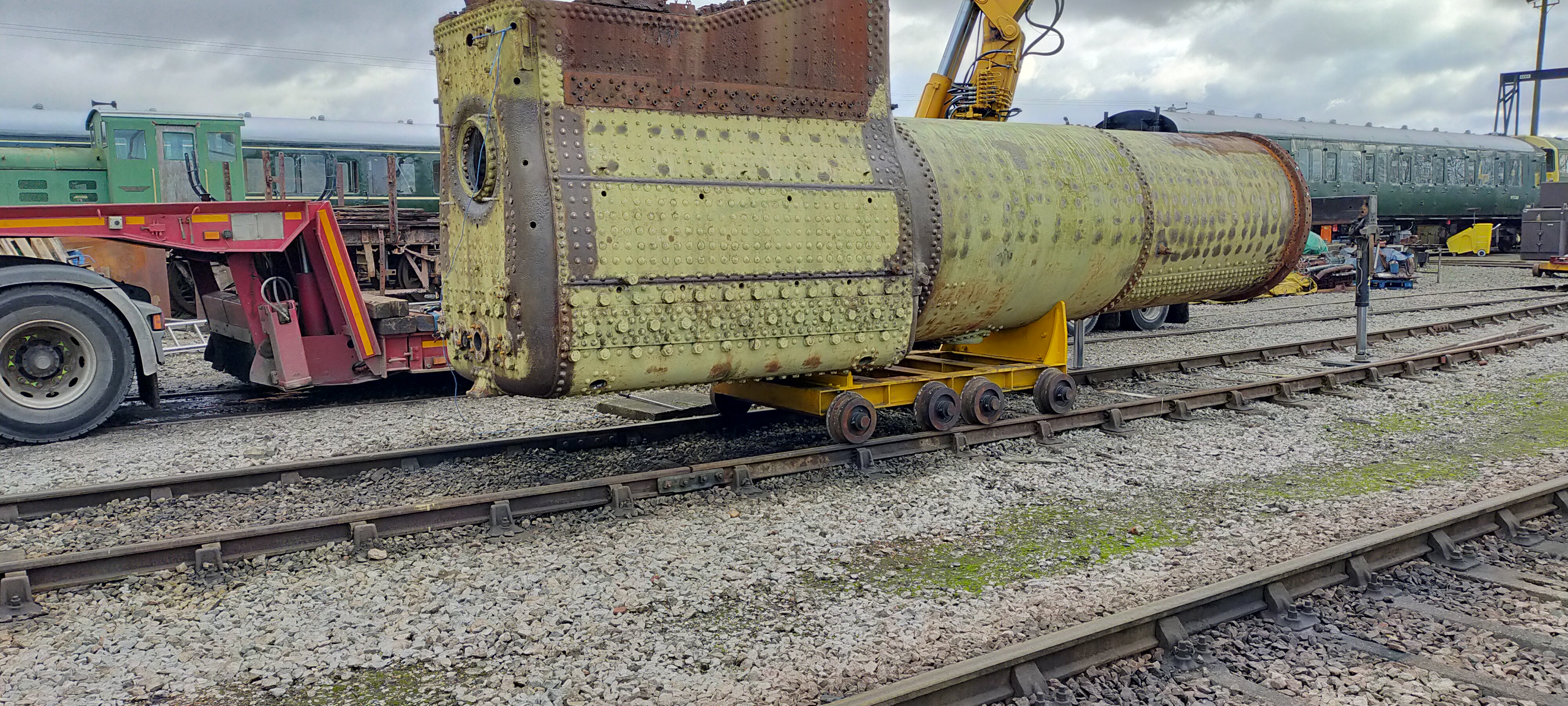